In Bristol, close to Severn Beach, sits one of the largest Amazon fulfilment centres in the UK. It is a 500,000 sqft building, as big as eight football pitches, with around 2000 employees who travel from across the country – even from Wales, which is just across the Severn Bridge – to ensure that your Amazon orders are packaged and quickly delivered to your doorstep.
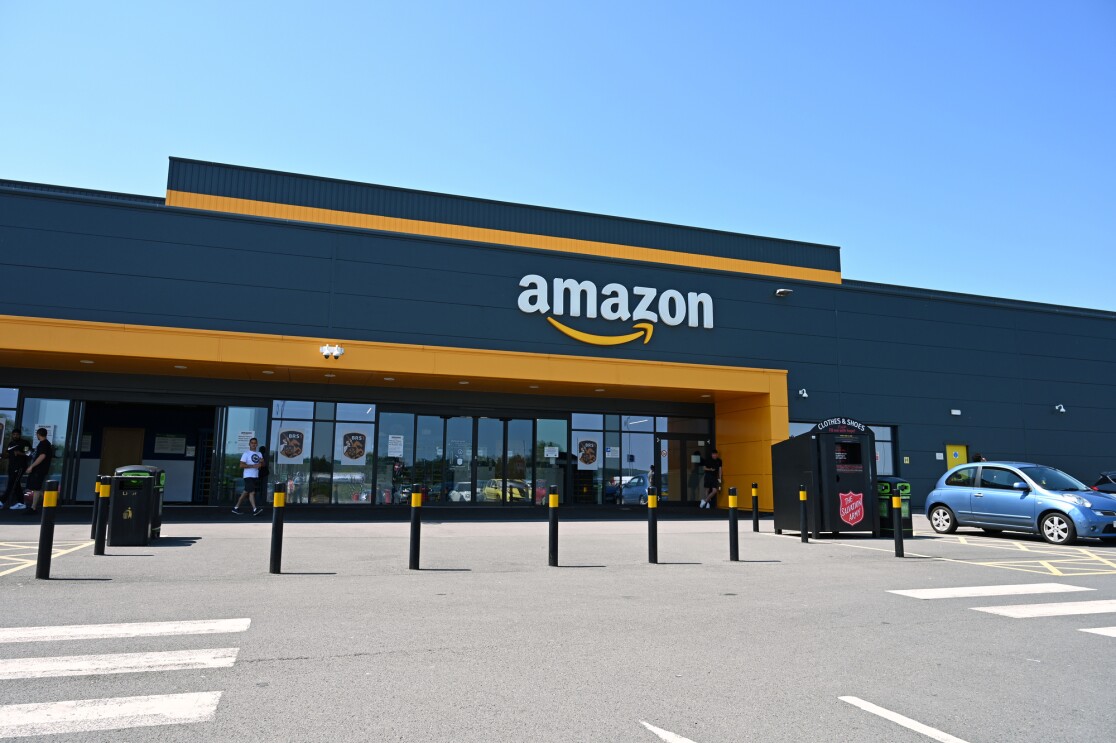
The fulfilment centre is one of many sites in the UK that use state-of-the-art robotics, solar panel installations, and many other high-tech pieces of machinery.
Join me for a whistle-stop tour around the cutting-edge facility and see the unique process of how people, technology, and complex algorithms, pick, pack and ship millions of customer orders every year.
Before we get started, did you know that all Amazon sites across the world are named after the nearest international airport? Bristol Airport is the closest airport to the fulfilment centre, giving it an official designation of BRS1.
Welcome to Bristol and BRS1
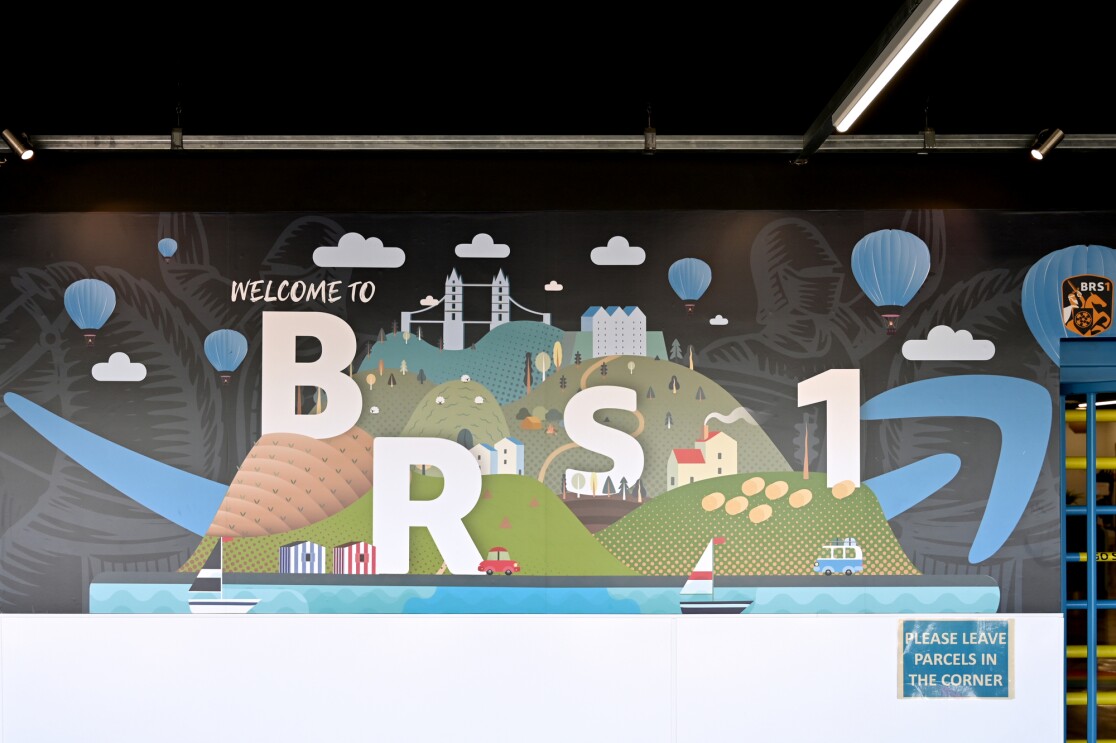
The first thing visitors see at BRS1 is a mural depicting Bristol’s iconic landmarks and sights like Clifton Suspension Bridge, Bristol Castle, Hot Air Balloons, Severn Beach, and the River Severn. Look closer and you’ll even spot the vague outline of a knight, a recurring theme you’ll pick up on throughout the fulfilment centre which is perhaps a nod to the history of the Knights Templar in Bristol. The mural provides an instant sense of Bristol’s beauty and rich history – even when away from the hustle and bustle of the city.
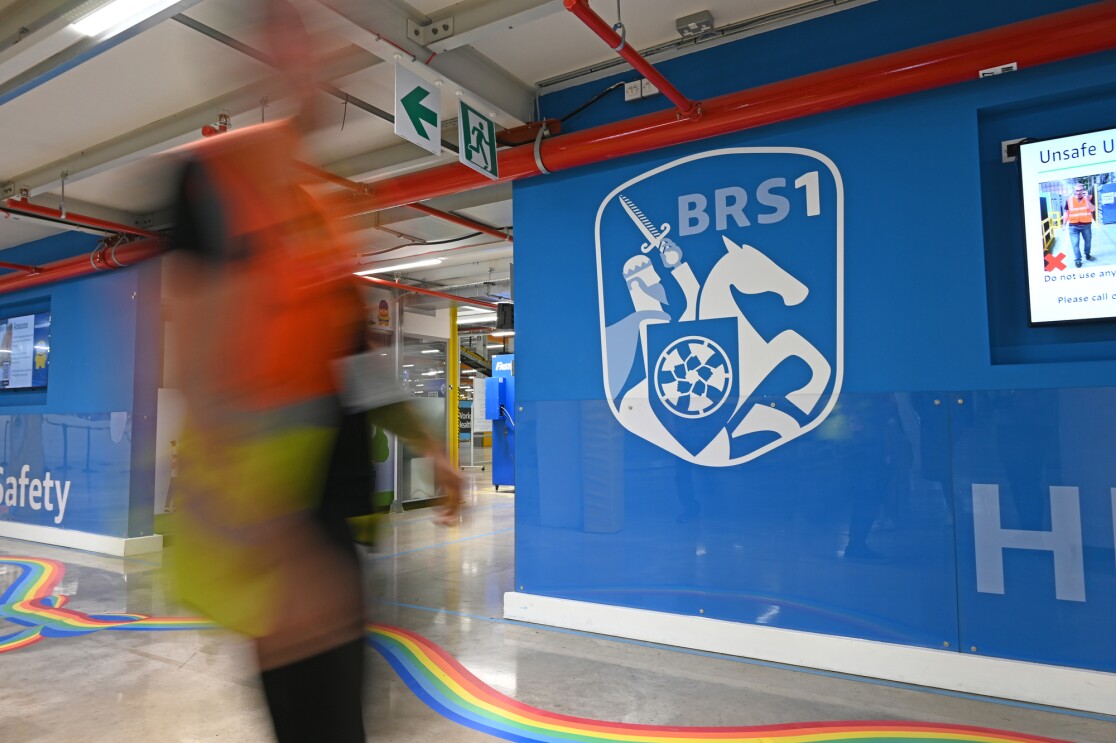
First glance inside
As soon as I walked past the revolving metal gates, I was in awe of the sheer size of BRS1. Past the reception area, I could see the massive scale of the operation with huge conveyor belts, large boxes and busy employees.
I spoke to the receptionist to register as a guest, and as I waited for my tour guide to meet me, I took a quick scan of the waiting area. To my left was a brightly coloured cafeteria and to my right was a games area with ping pong and table tennis for employees to have fun while on their break.
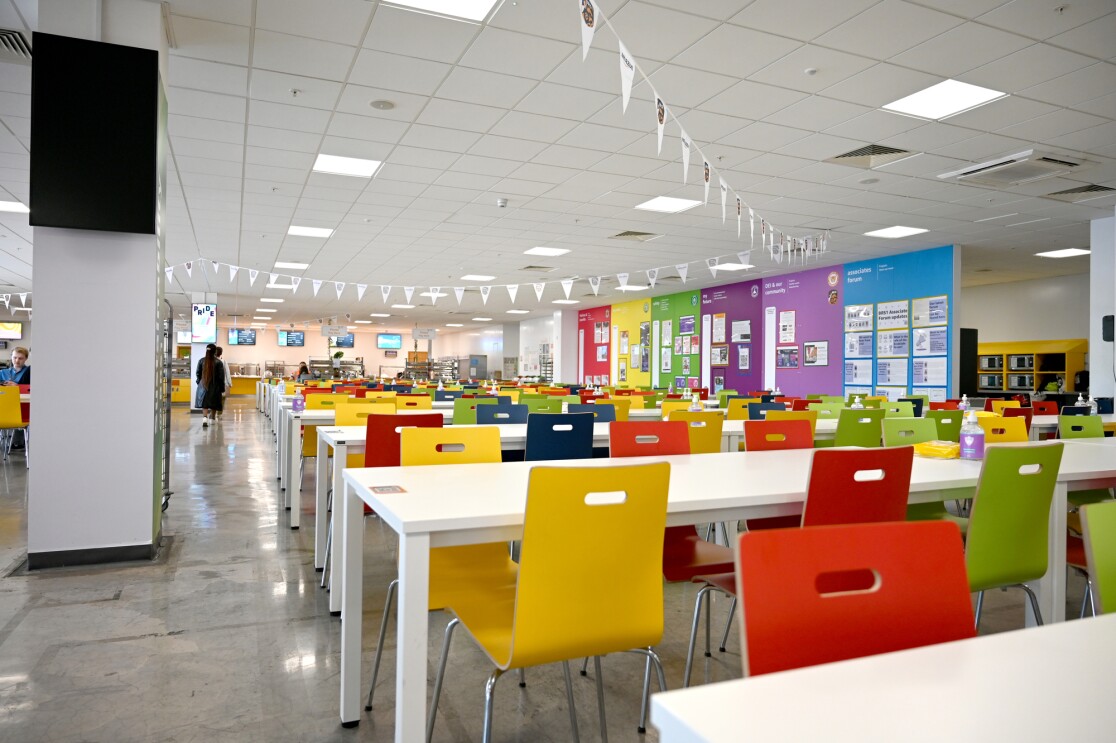
The atmosphere was electric with employees just returning from their break. It was hard not to join in as a group of employees walked past randomly singing 'Whole Again' by the noughties’ British girl group Atomic Kitten.
Once I checked in and was joined by my first guide, my tour of BRS1 officially began.
Meeting the Amazon Smart Robots
I was led to the busy communal office area to meet Reliability Maintenance Engineering (RME) technician Geraint Davies who meticulously looks after the robots in BRS1.
The busy open-plan office looked just like any other office – apart from the life-sized suit of armour standing in the middle. Or the gallery wall covered with caricature drawings of BRS1 employees.

Keeping with the knightly theme throughout the fulfilment centre, all of the meeting rooms are named after fictional and historical medieval figures like “Arthur” or “King Edward I”, alongside the BRS1 coat of arms.
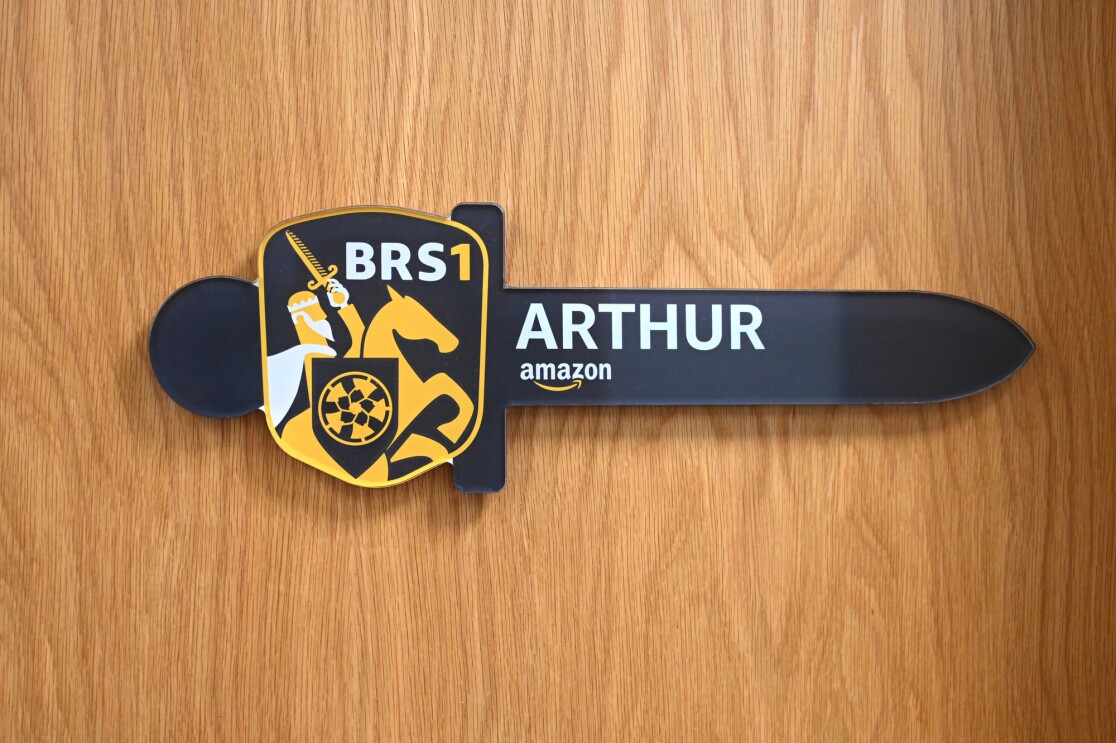
After a few minutes of waiting, Geraint arrived to take me to the floor where products that arrive at the fulfilment centre are put away – with Amazon smart robots helping employees every step of the way.
In the ‘Stow’ and ‘Pick’ areas, there are numerous workstations where employees store or pick items from huge, yellow-tiered pods that are transported to them by smart robots. BRS1 has more than 3000 robots that can lift products that weigh as much as a grand concert piano – that’s almost 1,400 lbs!
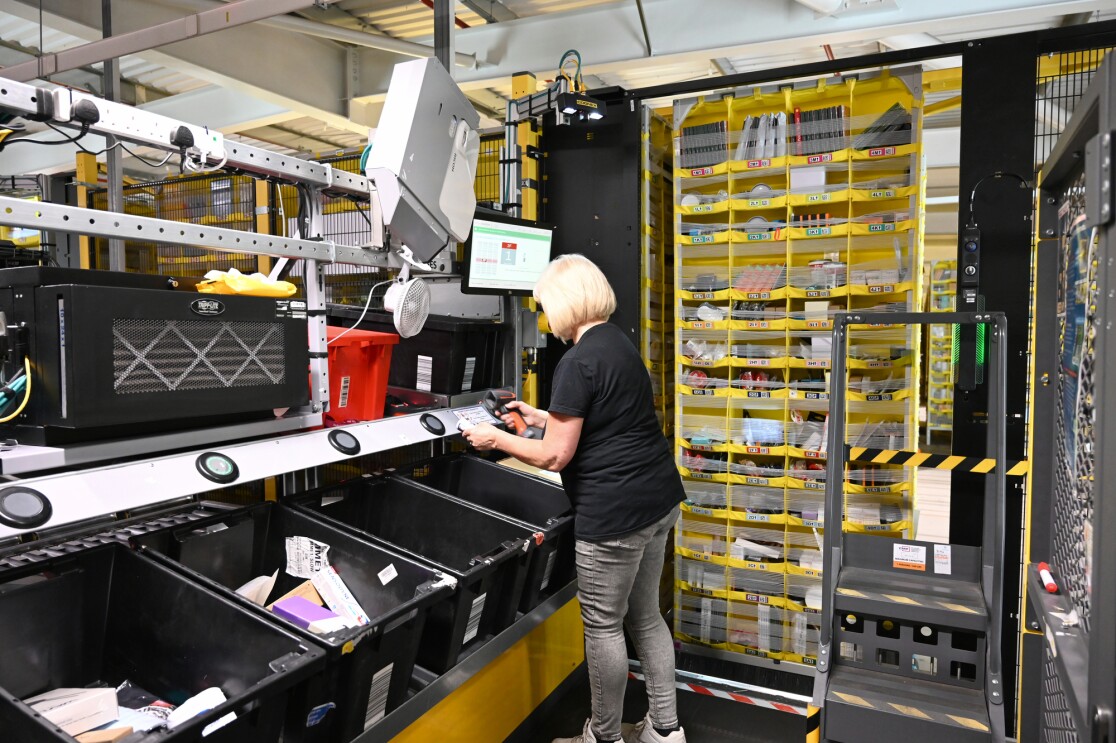
The robots are equipped with tiny cameras on the front and underneath to scan QR codes on the floor, enabling them to locate their position and avoid collisions with other robots as they move around the floor.
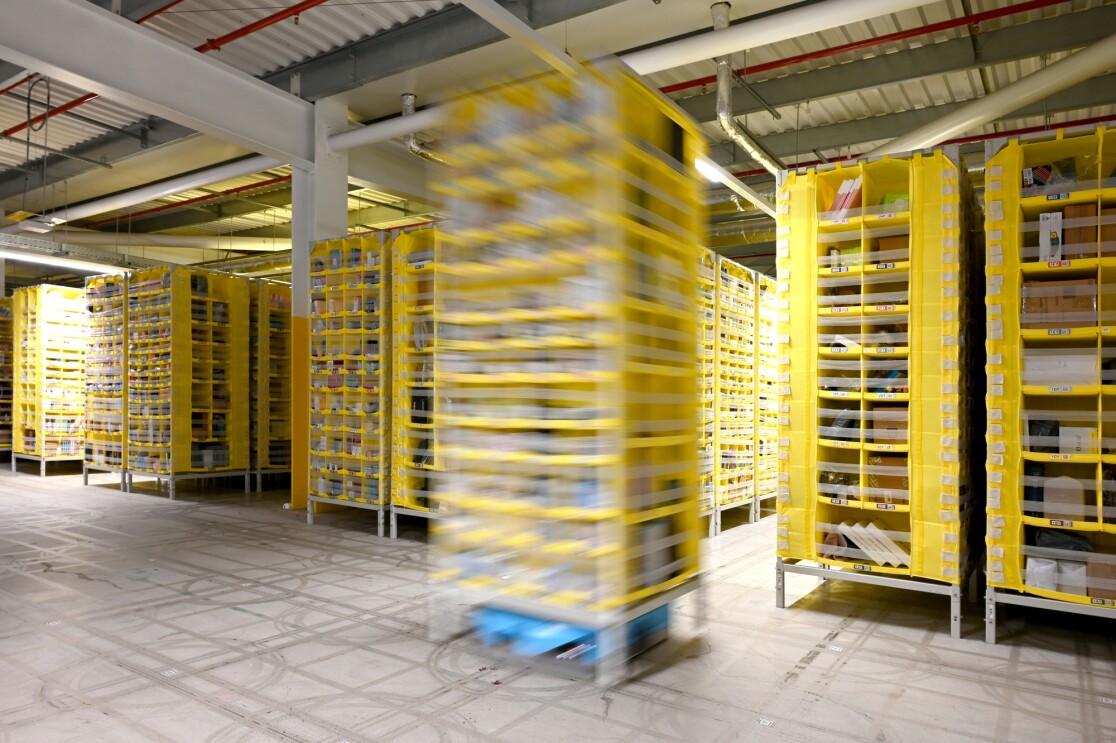
To ensure everyone’s safety, strict rules govern who can access the robots, but Geraint was more than happy to demonstrate how it all operates. He quickly donned a ‘Cerberus Vest’, which is an AI-powered safety vest and walked into the robotics zone. The vest connects to a tablet that displays the exact location of all the robots on the floor.
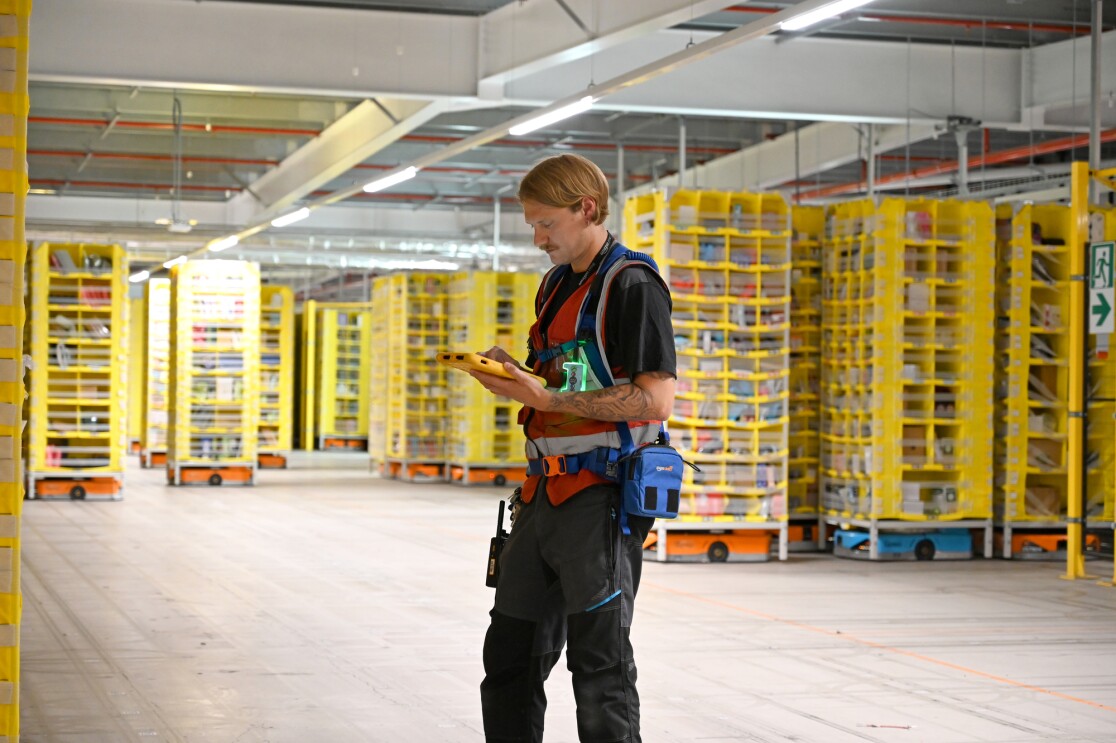
With the vest on, any robot near Geraint is prompted to slow down, change course or even stop completely. Geraint explained that the robots automatically move to a charging point when their batteries are low and are powered by the fulfilment centre’s solar panels.
Single and multi-packing with automated systems
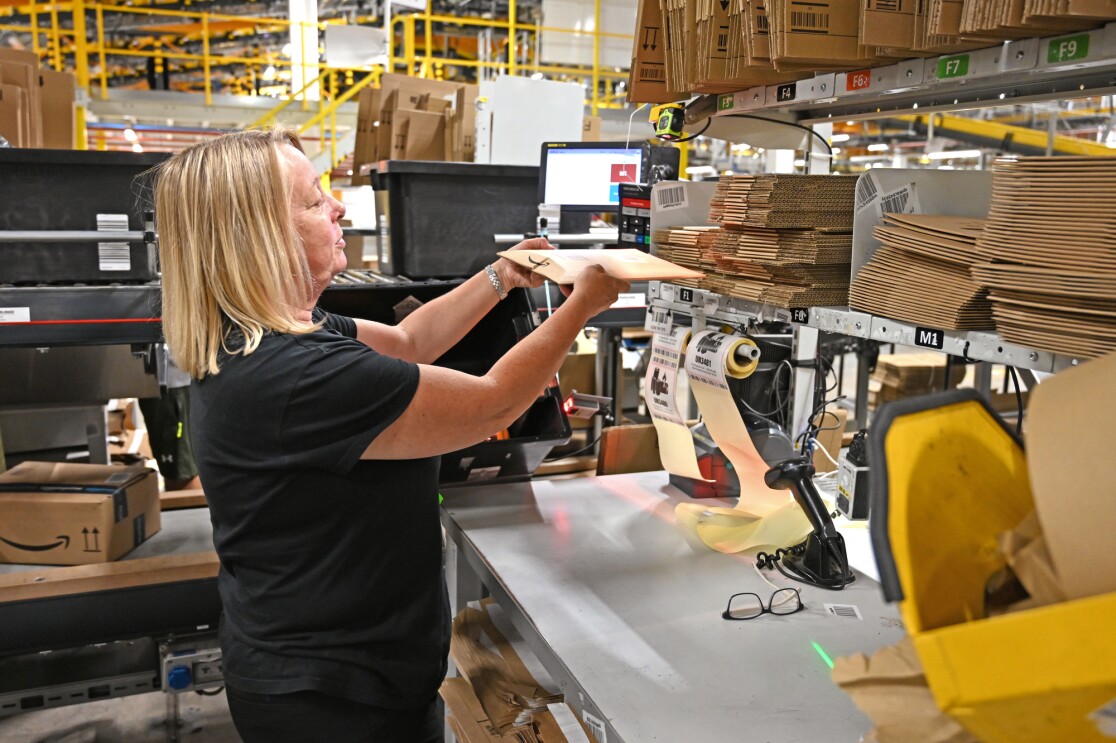
The next destination on my tour was the packaging section of the fulfilment centre where Amazon associates pack items in single or multiple packages. Each workstation is fully equipped with all the necessary materials, including a scanner, labels, and boxes in 14 different sizes. My new guide, Warehouse Associate Cheryl Knight, explained that as soon as the items are scanned, the system automatically determines the appropriate box and label size to ensure nothing is wasted. After packing, the items are conveyed onto SLAM (Scan, Label, Apply, Manifest) machines where shipping labels are applied, a quality control check is performed, and then they are moved to the final stage for shipment.
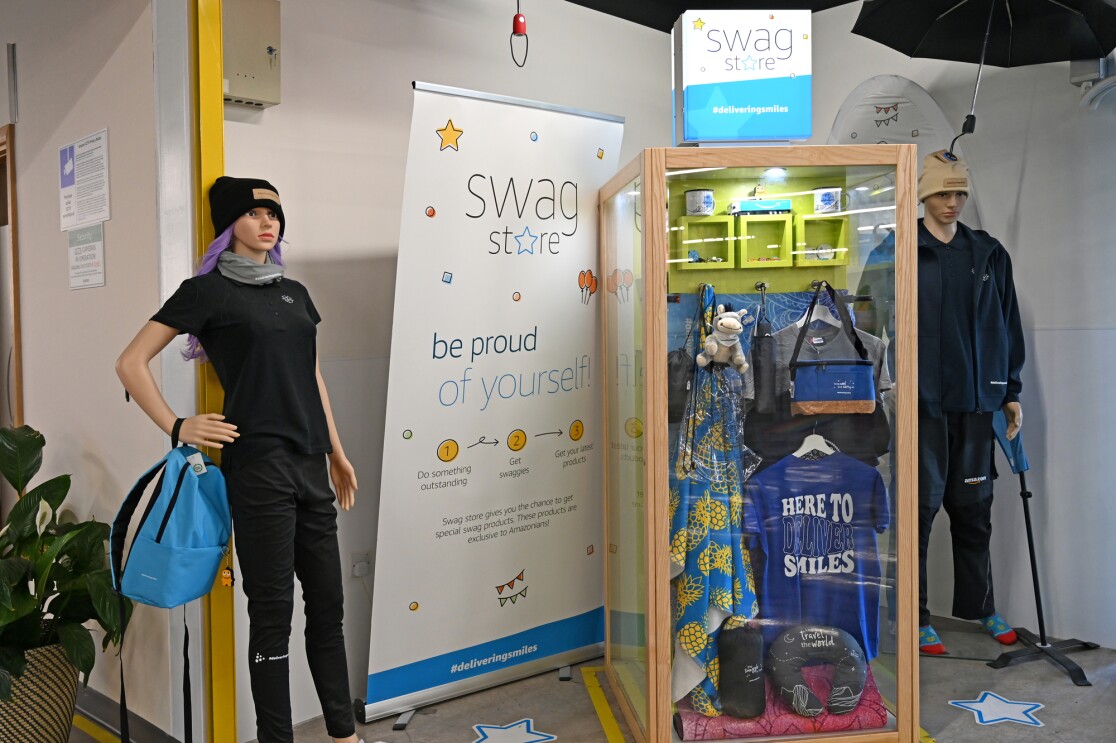
After completing the tour and returning to the reception, I spotted the ‘swag store’ with an array of exclusive items to commemorate a BRS1 visit like travel pillows, t-shirts, coffee mugs and even badges.
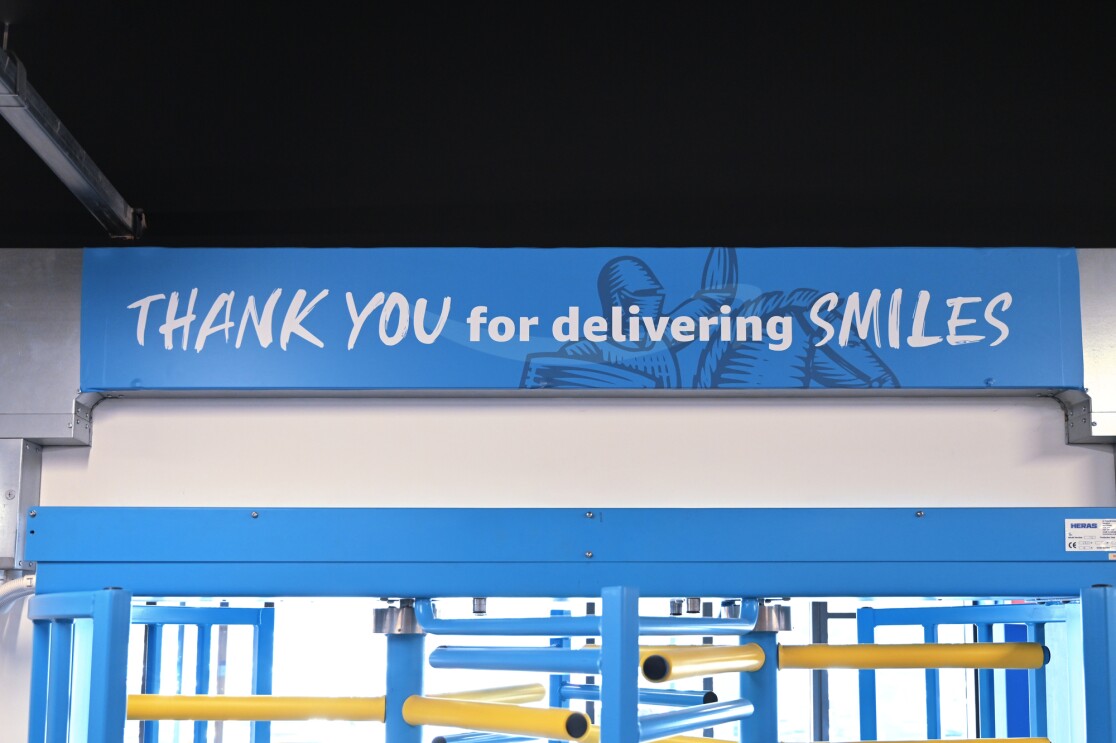
The atmosphere was still busy as I made my way out but it was great not only to hear the lively conversations but to have seen first-hand how the fulfilment centre’s passionate employees and cutting-edge technology work hand in hand to ensure that Amazon orders are fulfilled and delivered right to our doorsteps.
Interested in learning more about Amazon’s fulfilment centres? You can find out more about FCs or book your very own tour here.