The Fulfilment Centre (FC) Tours Programme usually offers public tours in 47 sites globally, allowing visitors to see what it’s like to work in an FC and also get a glimpse of the great technology and people that make Amazon what it is today. Each site provides free public tours at least twice per day, hosting many private groups consisting of schools, youth organisations, customers, businesses, media, politicians and more.
Due to an abundance of caution to protect employees and guests, and following developments relating to preventive measures taken for health in the region regarding the Coronavirus (COVID-19), Amazon made the decision to pause all Fulfilment Centre tours in Europe.
So this year the FC Tours teams are set to bring the tours to you, virtually over video!
If you’ve ever wondered how that product in your online shopping cart gets from Amazon to your door, find out more by watching the video and reading the highlights below.
Alternatively, we have just launched live virtual tours which are proving popular for our customers. To book a place, visit here.
*To turn on video captions, press the 'CC' icon next to the wheel within the viewing panel.
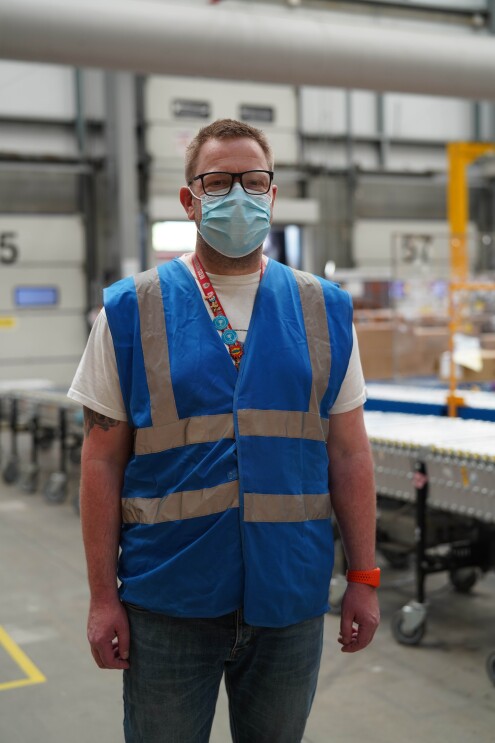
The whole process starts with people, technology and high tech computer algorithms
What a Fulfilment Centre looks like
Many centres span the equivalent of around 10 to 28 football pitches and can hold tens of millions of items on any given day. Amazon employees pick, pack, and ship customer orders at more than 175 similar facilities worldwide.
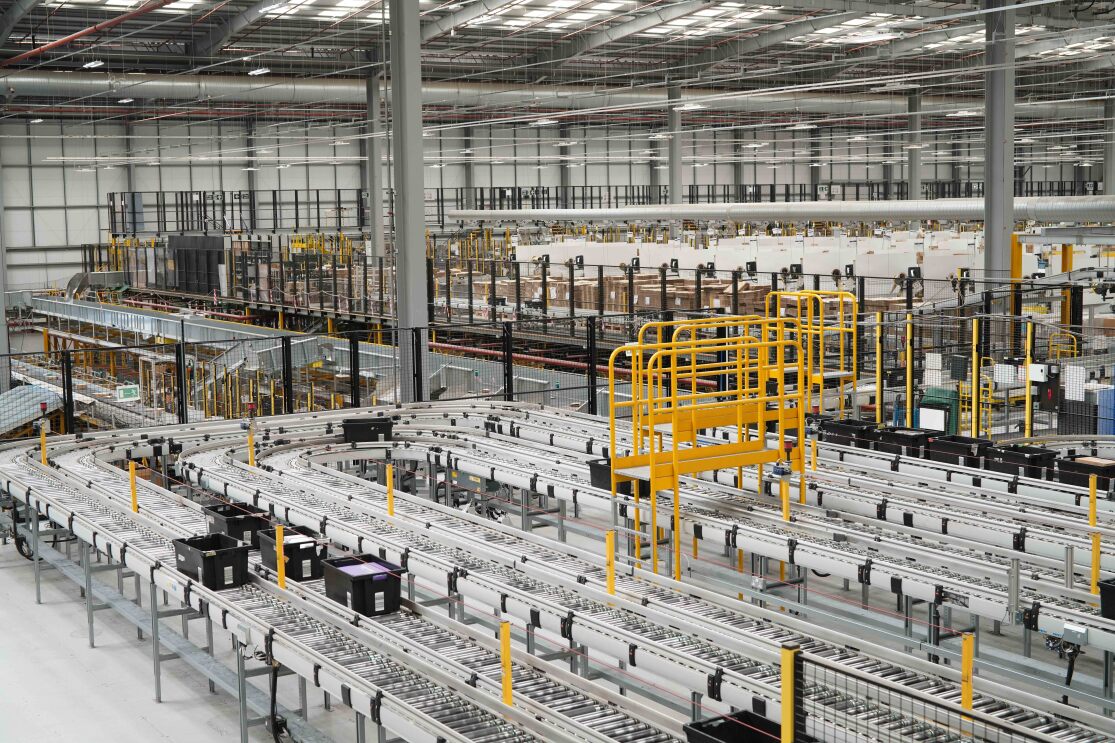
Fulfilment Centres take a combination of people and technology to operate and run smoothly. With a unique process in place, employees pick, pack and ship millions of customer orders items per year.
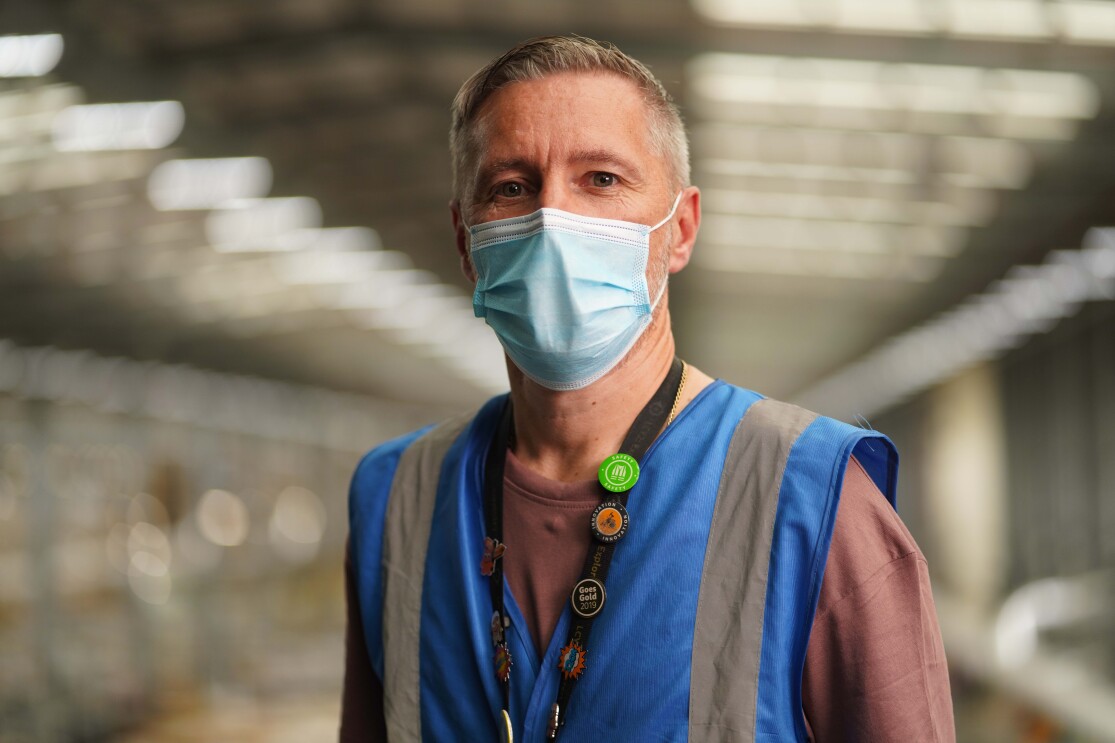
All of our buildings are named after international airports, such as BHX1 which is named after Birmingham International airport.
The stow process
When items from small and medium businesses are received into the Fulfiment Centre, they make their way through to the stowing process. Instead of storing items as a retail store would—electronics on one aisle, books on another—all of the inventory at Amazon fulfilment centres is stowed randomly.
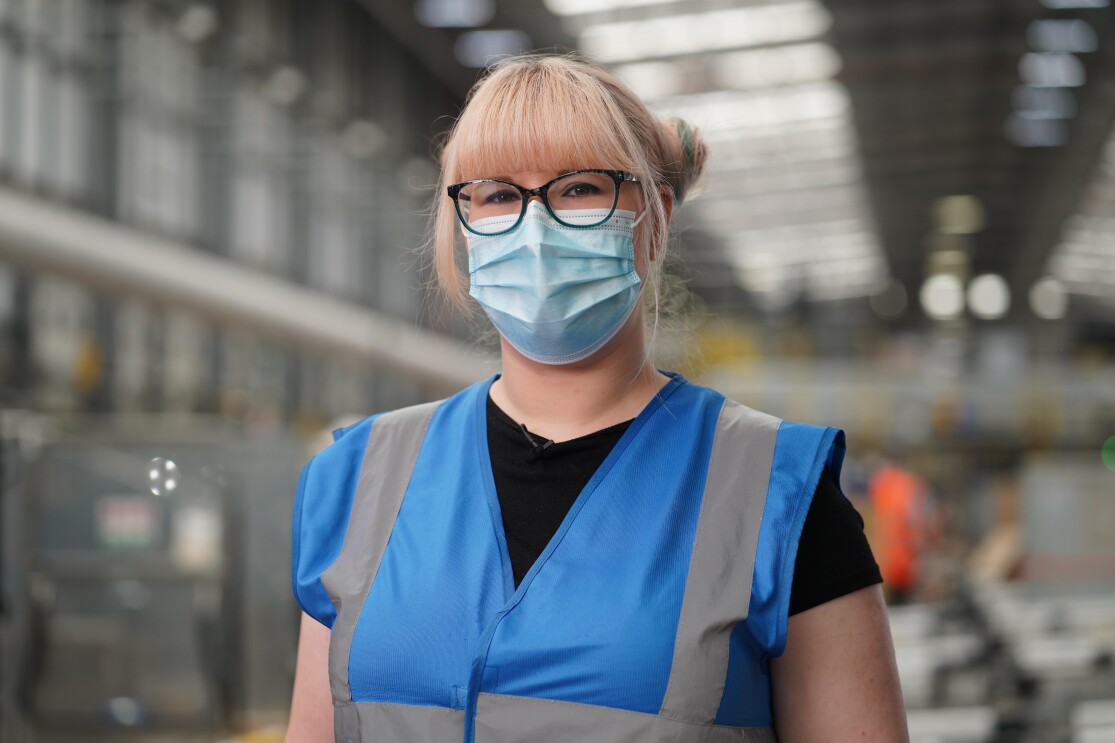
This method of stowing has been very successful and over recent years we have developed something even more exciting.
Smart Amazon Robots
Robots ferry these pods to associates at stow stations based on product size, navigating 2D barcodes on the floor and yielding way to one another depending on which has more pressing business.
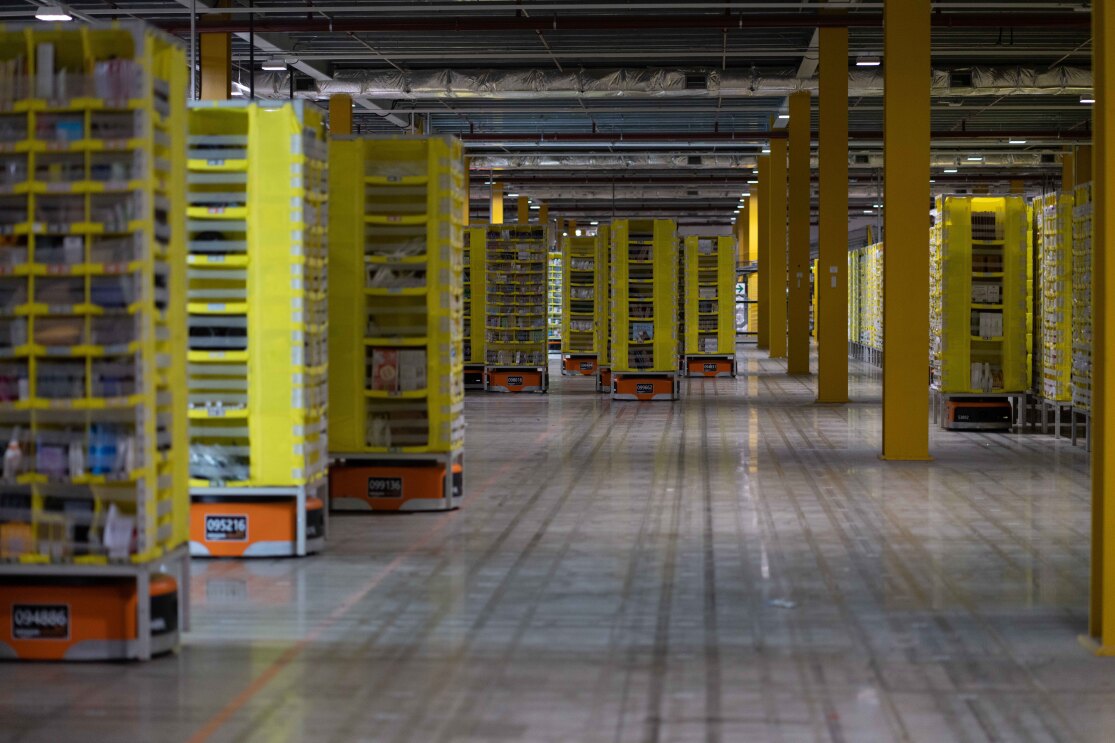
Yellow, tiered "pods" stack bins full of unrelated items, all of them tracked by computers. This counterintuitive method actually makes it easier for associates to quickly pick and pack a wide variety of products.
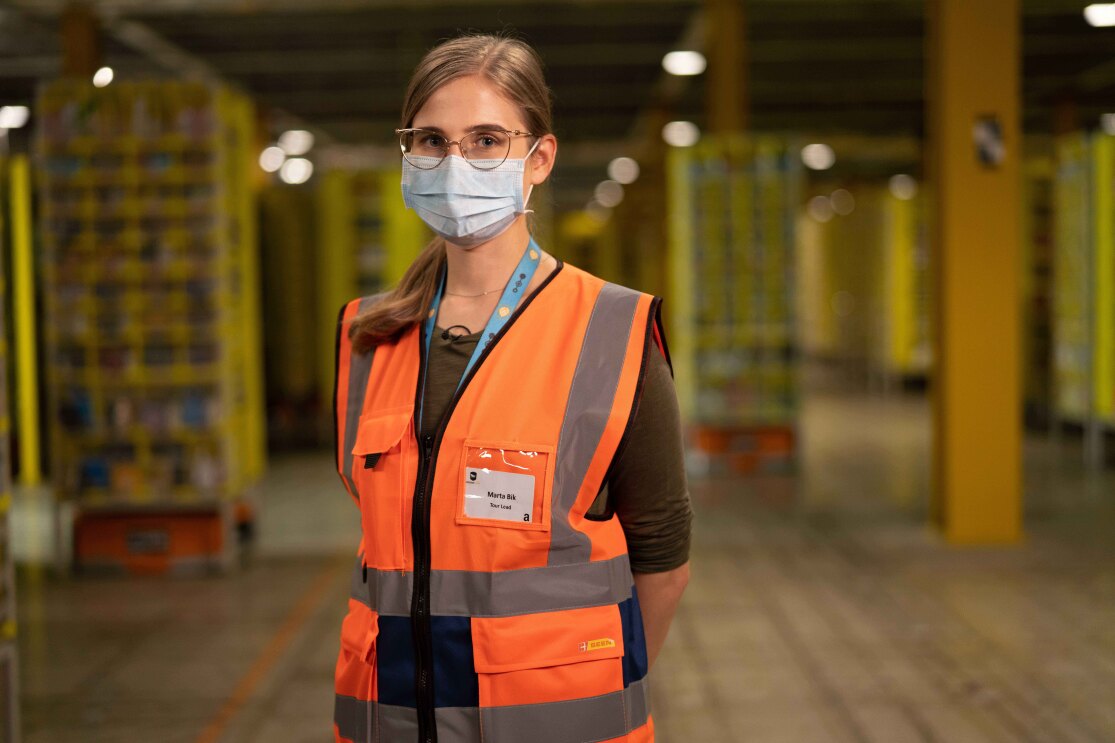
Robots are informed about which item has been ordered and where it is located, they then collect and bring it to our working station.
Shipping out orders with SLAM
After quality assurance is carried out and items are packed, they then going through SLAM (Scan, Label, Apply, Manifest) machines. This is where shipping labels with astonishing speed are applied, contrary to the name, a light touch. For quality control, the package is weighed to make sure the contents match the order.
A shipping sorter reads package labels to determine where and how fast customer orders should be sent, and then they are on their way to the final stage to be shipped out.
Join our #AmazonFCTours team as they guide you on a guided video tour of one of our Fulfilment Centres.